Plan de Maintenance des Équipements Statiques Automatisé et Personnalisable dans Excel
Les équipements statiques sont essentiels dans de nombreux processus industriels, bien qu’ils n’aient pas de parties mobiles. Ils subissent néanmoins des pannes récurrentes, dues principalement à des facteurs environnementaux et à des contraintes mécaniques. Parmi les pannes les plus fréquentes, on trouve la corrosion, qui résulte de l’exposition des matériaux à des éléments agressifs comme l’humidité ou les produits chimiques. Les fuites sont également courantes, souvent causées par des joints défectueux ou une pression excessive dans les réservoirs et conduites.
Un autre problème récurrent est la fatigue des matériaux, qui se manifeste par la formation de fissures à cause de cycles de charge répétée. L’encrassement (ou fouling) est une autre cause fréquente de panne, notamment dans les équipements tels que les échangeurs de chaleur, où l’accumulation de dépôts réduit l’efficacité. De plus, la détérioration des revêtements expose les équipements à des dommages plus importants.
Les fissures et fractures peuvent se former dans les soudures ou les joints sous contrainte, tandis que la dilatation et contraction thermique due aux fluctuations de température provoquent des déformations ou des fissures. Enfin, les déformations surviennent lorsque des matériaux sont soumis à des contraintes au-delà de leur capacité mécanique, souvent en raison de surcharges ou de mauvaises conceptions.
Pour prévenir ces pannes, il est essentiel de mettre en place une maintenance préventive, d’effectuer des inspections régulières et d’utiliser des tests non destructifs pour surveiller l’état des équipements et intervenir avant que les problèmes ne deviennent critiques.
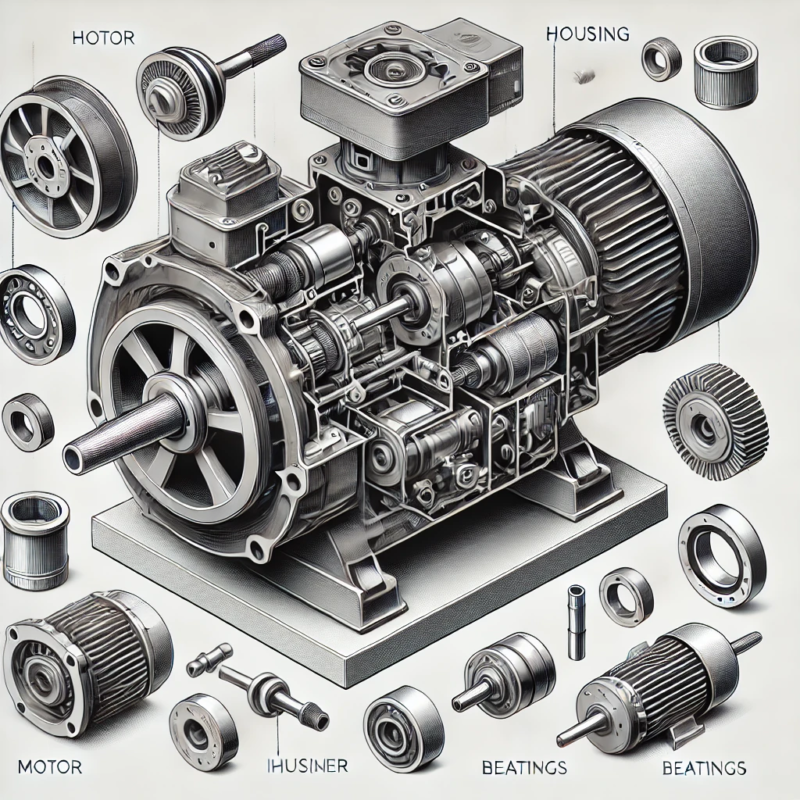
Voici un modèle de plan de maintenance pour les équipements statiques en plusieurs étapes. Il peut être adapté en fonction des besoins spécifiques de chaque équipement, mais il inclut les principales actions de maintenance préventive et corrective.
Plan de Maintenance des Équipements Statiques
1. Inspection Visuelle Générale
- Fréquence : Trimestrielle
- Description :
- Vérifier l’intégrité structurelle des équipements (absence de fissures, déformations).
- Rechercher des signes de corrosion, détérioration des soudures, et présence de fuites.
- Identifier toute décoloration ou anomalie visible sur les surfaces des réservoirs, conduites ou échangeurs de chaleur.
- Responsable : Technicien de maintenance
- Objectif : Détecter les anomalies visibles avant qu’elles ne deviennent des pannes majeures.
2. Nettoyage des Surfaces
- Fréquence : Semestrielle
- Description :
- Nettoyer les surfaces externes des réservoirs, tuyaux, et échangeurs de chaleur.
- Éliminer les dépôts de sédiments et les produits chimiques accumulés sur les équipements.
- Enlever les débris ou saletés pouvant causer l’obstruction des conduites.
- Responsable : Technicien de maintenance
- Objectif : Prévenir l’accumulation de substances corrosives ou nuisibles et améliorer l’efficacité du fonctionnement.
3. Contrôle de la Corrosion
- Fréquence : Annuellement
- Description :
- Inspecter les revêtements anticorrosion et les repeindre si nécessaire.
- Mesurer l’épaisseur des parois des réservoirs et conduites pour détecter l’usure due à la corrosion.
- Remplacer les parties gravement corrodées ou affaiblies.
- Responsable : Ingénieur corrosion/Inspecteur certifié
- Objectif : Prolonger la durée de vie des équipements en ralentissant le processus de corrosion.
4. Vérification des Joints et Soudures
- Fréquence : Semestrielle
- Description :
- Inspecter les joints d’étanchéité et les soudures pour détecter les fuites et fissures.
- Tester les joints pour vérifier leur capacité d’étanchéité sous pression.
- Réparer ou remplacer les soudures et joints défectueux.
- Responsable : Soudeur/Inspecteur qualifié
- Objectif : Maintenir l’intégrité des soudures et joints pour éviter les fuites et les défaillances.
5. Test de Pression et d’Étanchéité
- Fréquence : Annuellement ou après chaque réparation majeure
- Description :
- Effectuer un test hydrostatique pour vérifier la résistance des réservoirs et tuyaux à la pression.
- Contrôler l’étanchéité des équipements sous pression pour détecter d’éventuelles fuites.
- Responsable : Ingénieur/Technicien qualifié
- Objectif : Garantir la capacité des équipements à fonctionner sous haute pression sans risque de rupture.
6. Entretien des Revêtements de Protection
- Fréquence : Tous les 2 ans
- Description :
- Vérifier l’état des revêtements thermiques et les réappliquer si nécessaire.
- Contrôler les couches d’isolation des réservoirs et équipements exposés à des variations extrêmes de température.
- Responsable : Spécialiste en revêtements/Technicien maintenance
- Objectif : Prévenir les pertes thermiques et les dommages dus aux températures extrêmes.
7. Contrôle Non Destructif (CND)
- Fréquence : Selon l’usure ou les recommandations de l’inspecteur (au moins tous les 2 ans)
- Description :
- Effectuer des tests par ultrasons, radiographie ou magnétoscopie pour détecter des fissures internes ou des défaillances non visibles.
- Réaliser un contrôle par ressuage pour identifier les microfissures en surface.
- Responsable : Inspecteur certifié en CND
- Objectif : Identifier les fissures ou faiblesses structurelles avant qu’elles ne causent des ruptures critiques.
8. Vérification des Supports et Fixations
- Fréquence : Trimestrielle
- Description :
- Inspecter les supports, brides, et fixations des équipements statiques pour s’assurer qu’ils sont bien serrés et en bon état.
- Remplacer les supports endommagés ou corrodés.
- Responsable : Technicien de maintenance
- Objectif : Garantir la stabilité des équipements et prévenir les mouvements ou déformations dus à des fixations défectueuses.
9. Suivi et Enregistrement des Données
- Fréquence : Après chaque intervention
- Description :
- Documenter toutes les inspections et interventions de maintenance dans un rapport.
- Tenir à jour un historique de maintenance pour chaque équipement statique.
- Utiliser les données collectées pour anticiper les interventions futures.
- Responsable : Responsable maintenance
- Objectif : Améliorer la gestion des équipements en utilisant les données pour mieux planifier les futures interventions.
10. Renforcement ou Remplacement des Équipements
- Fréquence : Selon les résultats des inspections et les recommandations des experts
- Description :
- Remplacer les équipements statiques ou parties d’équipement trop usés ou endommagés pour garantir la sécurité.
- Renforcer les zones critiques sujettes à la fatigue des matériaux.
- Responsable : Ingénieur structure/Technicien
- Objectif : Prolonger la durée de vie des équipements et prévenir les incidents majeurs.
Ce plan de maintenance des équipements statiques est conçu pour prolonger leur durée de vie, garantir leur sécurité et éviter les pannes imprévues. Il repose sur une combinaison d’inspections visuelles régulières, de tests non destructifs, et d’interventions spécifiques sur les éléments critiques comme les joints, soudures, et revêtements. Un bon suivi des interventions et des enregistrements systématiques permettront d’adapter le plan en fonction de l’évolution des équipements.
