Maintenance Préventive : Types, KPIs, Mise en Œuvre et Outils Essentiels
La maintenance préventive est une approche stratégique qui vise à assurer la durabilité des équipements industriels, à optimiser les performances des machines et à éviter les pannes coûteuses. Contrairement à la maintenance corrective, qui intervient après une défaillance, la maintenance préventive repose sur l’anticipation et la planification des interventions avant qu’un problème ne survienne.
Cet article explore en profondeur les types de maintenance préventive, les indicateurs clés de performance (KPIs) pour en mesurer l’efficacité, les étapes de mise en œuvre ainsi que les outils et tableaux nécessaires pour un suivi efficace.
1. Types de Maintenance Préventive
La maintenance préventive se décline en plusieurs catégories en fonction des besoins et des équipements concernés. On distingue principalement :
1.1 Maintenance Systématique
Il s’agit d’une maintenance planifiée à des intervalles réguliers, indépendamment de l’état réel de l’équipement. Elle repose sur des recommandations du fabricant et des expériences d’exploitation.
Exemples :
- Changement d’huile et de filtres sur un moteur chaque 500 heures de fonctionnement.
- Inspection trimestrielle des systèmes électriques.
1.2 Maintenance Conditionnelle
Elle repose sur des contrôles réguliers et l’analyse des données en temps réel pour déterminer le moment opportun pour une intervention. Cette approche évite les arrêts inutiles et optimise les coûts.
Exemples :
- Surveillance des vibrations d’un moteur via un capteur pour anticiper un défaut.
- Utilisation de caméras thermiques pour détecter une surchauffe anormale.
1.3 Maintenance Prédictive
Grâce aux nouvelles technologies (IoT, Intelligence Artificielle, Big Data), la maintenance prédictive repose sur des modèles d’analyse avancée pour anticiper les pannes avec précision.
Exemples :
- Analyse des tendances de température et de pression d’un compresseur.
- Utilisation de capteurs connectés pour évaluer la détérioration d’un roulement.
1.4 Maintenance Préventive Améliorative
Elle vise à améliorer la conception des équipements pour réduire les besoins de maintenance et augmenter leur durée de vie.
Exemple :
- Modification d’un système hydraulique pour diminuer le risque de fuite.
2. KPIs pour Suivre la Performance de la Maintenance Préventive
Pour évaluer l’efficacité d’une stratégie de maintenance préventive, plusieurs indicateurs clés de performance (KPIs) sont utilisés :
2.1 Taux de Disponibilité des Équipements (Availability Rate)
Cet indicateur permet de savoir combien de temps un équipement est opérationnel par rapport au temps total prévu.

2.2 MTBF (Mean Time Between Failures)
Il mesure la fiabilité d’un équipement en déterminant la durée moyenne entre deux pannes.

2.3 MTTR (Mean Time To Repair)
Il permet d’évaluer l’efficacité des interventions de maintenance.

2.4 Coût de Maintenance Préventive vs Corrective
Comparer les coûts de maintenance préventive avec ceux des réparations permet d’évaluer la rentabilité de la stratégie adoptée.
3. Comment Mettre en Œuvre une Stratégie de Maintenance Préventive
Étape 1 : Identification des Équipements Critiques
Tous les équipements ne nécessitent pas le même niveau d’attention. Il est essentiel de classer les équipements selon leur importance et leur impact sur la production.
Étape 2 : Création d’un Plan de Maintenance
Un plan de maintenance détaillé doit être établi pour chaque équipement, en précisant :
- La fréquence des interventions.
- Les actions à réaliser (inspection, lubrification, remplacement de pièces, etc.).
- Les ressources nécessaires.
Étape 3 : Utilisation d’un Système de GMAO (Gestion de Maintenance Assistée par Ordinateur)
Un logiciel de GMAO permet d’automatiser les tâches de maintenance, d’optimiser le suivi des interventions et de stocker l’historique des pannes et des réparations.
Étape 4 : Suivi des Indicateurs et Amélioration Continue
L’analyse régulière des KPIs permet d’ajuster la stratégie de maintenance et d’améliorer continuellement la performance des équipements.
4. Outils et Tableaux Essentiels pour la Maintenance Préventive
4.1 Tableau de Suivi des Interventions
Un tableau Excel ou un logiciel de GMAO peut être utilisé pour suivre l’historique des maintenances.
Équipement | Date de l’intervention | Type de Maintenance | Intervenant | Temps d’arrêt | Remarques |
---|---|---|---|---|---|
Compresseur 1 | 01/02/2024 | Conditionnelle | Technicien A | 30 min | RAS |
Machine X | 05/02/2024 | Systématique | Technicien B | 45 min | Changement de filtre |
4.2 Plan de Lubrification
Un planning de lubrification permet de s’assurer que chaque pièce mécanique reçoit le bon entretien à la bonne fréquence.
4.3 Diagramme de Pareto des Pannes
L’utilisation d’un diagramme de Pareto permet d’identifier les principales causes de pannes et de concentrer les efforts de maintenance sur les plus critiques.
5. Visuels et Schémas pour une Meilleure Compréhension
Pour accompagner la stratégie de maintenance préventive, des éléments visuels tels que :
- Des schémas techniques d’équipements montrant les points de contrôle.
- Un diagramme de Gantt pour le suivi des interventions.
- Des infographies illustrant les gains en productivité et la réduction des coûts grâce à la maintenance préventive.
Synthèse
La maintenance préventive est un levier puissant pour améliorer la fiabilité des équipements, optimiser les coûts et réduire les temps d’arrêt.
L’adoption d’une stratégie de maintenance préventive efficace repose sur la compréhension des besoins spécifiques des équipements, le suivi rigoureux des interventions et l’utilisation d’outils adaptés. Investir dans cette approche permet d’améliorer la productivité tout en minimisant les coûts de maintenance corrective.
🔧 Votre prochaine étape ? Mettez en place un plan de maintenance et commencez à suivre vos KPIs dès aujourd’hui pour une gestion efficace de vos équipements !
le Tableau Comparatif des Types de Maintenance Préventive
Le tableau comparatif met en évidence les différences fondamentales entre la maintenance systématique, conditionnelle et prévisionnelle. Voici les principaux points à retenir :
1️⃣ Maintenance Systématique
- Approche simple et planifiée à intervalles fixes.
- Assure une maintenance régulière, mais peut engendrer des coûts inutiles si les pièces ne sont pas encore usées.
- Idéale pour les équipements dont l’usure est bien connue et prévisible.
2️⃣ Maintenance Conditionnelle
- Basée sur l’analyse en temps réel de l’état des équipements.
- Permet de réduire les interventions inutiles et d’optimiser la durée de vie des pièces.
- Requiert l’installation de capteurs et une surveillance constante.
3️⃣ Maintenance Prévisionnelle
- Utilise des technologies avancées (IoT, IA, Big Data) pour anticiper les pannes.
- Offre une précision optimale et minimise les interruptions de production.
- Implique un investissement initial élevé, mais permet des économies importantes à long terme.
🔹 Conclusion :
La maintenance systématique convient aux équipements simples et prévisibles, tandis que la maintenance conditionnelle et prévisionnelle sont plus adaptées aux industries où l’optimisation des coûts et la réduction des arrêts non planifiés sont des enjeux majeurs. L’idéal est souvent un mix des trois approches, adapté aux besoins spécifiques de chaque entreprise. 🚀
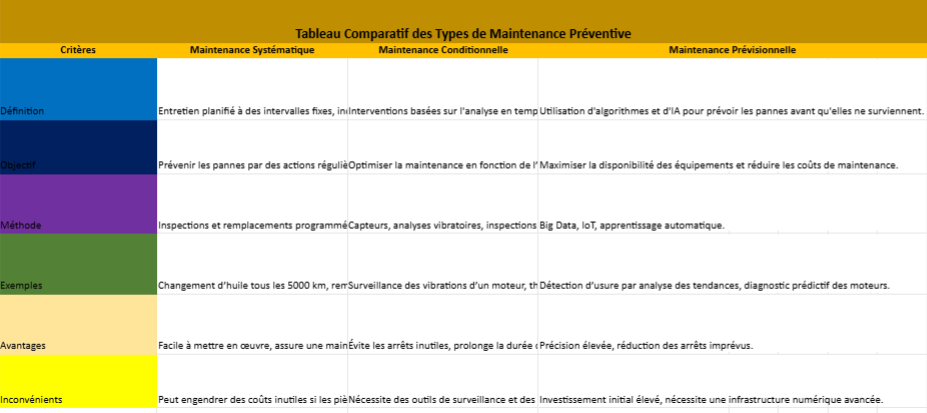
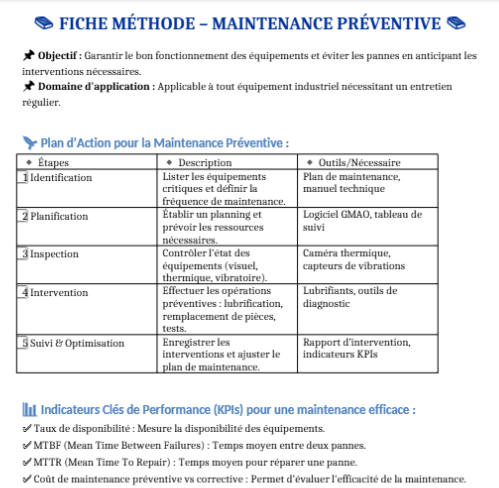
Étude de Cas : Optimisation de la Maintenance Préventive dans une Usine de Production
1. Introduction
L’entreprise Mécanotech est un fabricant de composants mécaniques pour l’industrie automobile. Elle utilise des machines-outils de haute précision qui nécessitent un entretien régulier. Cependant, l’entreprise faisait face à des pannes fréquentes, entraînant des arrêts de production coûteux.
L’objectif de cette étude de cas est de montrer comment la mise en place d’une stratégie de maintenance préventive optimisée a permis d’améliorer la disponibilité des équipements et de réduire les coûts de maintenance.
2. Problématique
Avant l’implémentation d’un programme de maintenance préventive structuré, Mécanotech rencontrait plusieurs problèmes :
- Une augmentation des pannes (MTBF faible) affectant la productivité.
- Des coûts de maintenance élevés, principalement en maintenance corrective (interventions en urgence).
- Un manque de suivi des équipements et une planification de maintenance inexistante.
- Des arrêts de production non planifiés, réduisant la capacité de livraison aux clients.
L’entreprise souhaitait améliorer la fiabilité de ses équipements en instaurant une maintenance préventive efficace.
3. Mise en Place d’une Stratégie de Maintenance Préventive
L’équipe de maintenance a mis en œuvre un plan d’action structuré en plusieurs étapes :
Étape 1 : Identification des équipements critiques
Une analyse des arrêts de production a permis d’identifier les équipements les plus sensibles :
- Machines CNC : Risque élevé de panne sur les moteurs et les systèmes de refroidissement.
- Compresseurs d’air : Indispensables au fonctionnement des outils pneumatiques.
- Systèmes hydrauliques : Souvent victimes de fuites et de variations de pression.
Étape 2 : Création d’un plan de maintenance préventive
Un planning détaillé a été mis en place avec différentes actions de maintenance :
- Maintenance systématique : Remplacement des filtres et vidanges des machines toutes les 500 heures de fonctionnement.
- Maintenance conditionnelle : Installation de capteurs de vibrations et de température pour surveiller l’état des moteurs.
- Maintenance prévisionnelle : Analyse des tendances grâce à un logiciel de GMAO (Gestion de Maintenance Assistée par Ordinateur).
Étape 3 : Suivi des interventions et analyse des KPIs
L’entreprise a défini plusieurs indicateurs clés de performance (KPIs) pour suivre l’impact de la maintenance préventive :
- MTBF (Mean Time Between Failures) : Augmentation du temps moyen entre deux pannes.
- MTTR (Mean Time To Repair) : Réduction du temps de réparation des équipements.
- Coût de maintenance préventive vs corrective : Mesure des économies réalisées.
4. Résultats et Bénéfices
Après 6 mois d’implémentation, l’entreprise a constaté des résultats significatifs :
Indicateur | Avant la maintenance préventive | Après 6 mois |
---|---|---|
Taux de disponibilité des équipements | 85% | 96% |
MTBF (heures entre pannes) | 200 h | 750 h |
MTTR (temps moyen de réparation) | 6 h | 2 h |
Coût de maintenance corrective | 70% du budget total | 35% du budget total |
Gains observés :
- 📉 Réduction des arrêts non planifiés de 40%, améliorant ainsi la productivité.
- 💰 Diminution de 25% des coûts de maintenance, notamment grâce à l’anticipation des pannes.
- 🏭 Augmentation de la durée de vie des équipements grâce aux interventions préventives régulières.
- ⚙️ Meilleure traçabilité des interventions via la GMAO, évitant les oublis et assurant un suivi précis.
5. Conclusion et Enseignements
L’implémentation d’une stratégie de maintenance préventive structurée a permis à Mécanotech d’améliorer la fiabilité de ses équipements et de réduire les coûts d’exploitation.
Leçons tirées :
✅ Une bonne planification de la maintenance réduit les interventions en urgence.
✅ L’utilisation de capteurs et de la GMAO améliore la précision des interventions.
✅ Le suivi des KPIs permet d’adapter et d’optimiser la stratégie de maintenance.
🔹 Prochaine étape ? Automatiser davantage l’analyse des données via l’intelligence artificielle et le machine learning pour une maintenance encore plus prédictive.
💡 Ce cas montre qu’une maintenance préventive bien pensée est un levier puissant pour améliorer la rentabilité et la performance des entreprises industrielles.
Glossaire de la Maintenance Préventive
Voici une liste des termes essentiels liés à la maintenance préventive, accompagnés de leurs définitions claires et précises.
A
- Analyse de Fiabilité (Reliability Analysis) : Évaluation des performances et du comportement d’un équipement en fonction de sa durée de vie et des conditions d’utilisation.
- Anomalie : Dysfonctionnement ou écart par rapport au fonctionnement normal d’un équipement.
B
- Benchmarking : Comparaison des performances des équipements et des processus avec des standards internes ou externes pour identifier les axes d’amélioration.
- Bilan de Maintenance : Rapport détaillant les interventions réalisées sur une période donnée afin d’évaluer l’efficacité de la maintenance.
C
- Capteur de Surveillance (Monitoring Sensor) : Dispositif permettant de mesurer des paramètres critiques (température, vibrations, pression) pour anticiper les pannes.
- CMMS (Computerized Maintenance Management System) : Système informatisé de gestion de la maintenance (GMAO en français).
- Coût de Maintenance Préventive : Ensemble des dépenses liées aux interventions planifiées pour éviter les pannes imprévues.
- Criticité des Équipements : Degré d’importance d’un équipement pour le bon fonctionnement du processus de production.
D
- Défaillance : Perte partielle ou totale de la fonction d’un équipement.
- Disponibilité : Indicateur de performance exprimant le pourcentage de temps où un équipement est opérationnel par rapport à son temps total de fonctionnement.
E
- Équipements Critiques : Machines ou composants essentiels au bon déroulement des opérations de production.
- État de Santé des Équipements : Évaluation de la condition physique et fonctionnelle d’un équipement en temps réel.
F
- Fiabilité (Reliability) : Probabilité qu’un équipement fonctionne sans panne pendant une période donnée.
- Fréquence de Maintenance : Intervalle de temps ou nombre d’heures de fonctionnement après lequel une intervention est réalisée.
G
- GMAO (Gestion de Maintenance Assistée par Ordinateur) : Logiciel permettant d’organiser, suivre et analyser les interventions de maintenance.
- Gestion des Pièces de Rechange : Processus de stockage et de suivi des composants nécessaires aux interventions de maintenance.
I
- Inspection : Contrôle visuel ou technique d’un équipement pour détecter des anomalies avant qu’une panne ne survienne.
- Intervention Planifiée : Maintenance réalisée selon un calendrier préétabli, sans attendre une défaillance.
K
- KPI (Key Performance Indicator) : Indicateurs de performance utilisés pour mesurer l’efficacité de la maintenance (MTBF, MTTR, taux de disponibilité, etc.).
L
- Lubrification : Application d’un lubrifiant (huile, graisse) pour réduire l’usure et les frottements entre pièces mécaniques.
M
- Maintenance Conditionnelle : Maintenance réalisée en fonction de l’état réel de l’équipement grâce à des capteurs et analyses.
- Maintenance Préventive : Ensemble des actions planifiées visant à éviter l’apparition de pannes.
- Maintenance Prédictive : Maintenance utilisant des outils avancés (IoT, intelligence artificielle) pour anticiper les défaillances avant qu’elles ne surviennent.
- Maintenance Systématique : Maintenance réalisée à des intervalles réguliers, indépendamment de l’état de l’équipement.
- MTBF (Mean Time Between Failures) : Temps moyen entre deux pannes consécutives d’un équipement.
- MTTR (Mean Time To Repair) : Temps moyen nécessaire pour réparer un équipement après une panne.
O
- Optimisation de la Maintenance : Processus d’amélioration continue visant à réduire les coûts et améliorer la disponibilité des équipements.
P
- Plan de Maintenance : Document détaillant les actions de maintenance préventive à réaliser sur chaque équipement.
- Panne : Arrêt imprévu d’un équipement nécessitant une intervention.
- Pièces d’Usure : Composants nécessitant un remplacement périodique (courroies, filtres, joints, etc.).
R
- Rapport d’Intervention : Document détaillant une opération de maintenance effectuée sur un équipement.
- Risque de Défaillance : Probabilité qu’un équipement tombe en panne dans un laps de temps donné.
S
- Stock de Maintenance : Ensemble des pièces de rechange disponibles pour assurer la maintenance des équipements.
- Stratégie de Maintenance : Approche adoptée par une entreprise pour optimiser la gestion de ses équipements et prolonger leur durée de vie.
T
- Taux de Disponibilité : Pourcentage du temps où un équipement est fonctionnel par rapport au temps total de production.
- Température Anormale : Signe précurseur de panne souvent surveillé via des capteurs thermiques.
V
- Vibrations Anormales : Oscillations inhabituelles d’un moteur ou d’une machine, souvent un signe d’usure ou de défaut mécanique.
Ce glossaire permet de mieux comprendre les termes essentiels liés à la maintenance préventive et d’optimiser son application en entreprise. ✅