Utilizing a Preventive Maintenance Dashboard Table Template for Enhanced Efficiency and Reliability
In this article, you will discover a table template for a Preventive Maintenance Dashboard.
Context:
The role of the preventive maintenance manager is of utmost importance in ensuring the operational efficiency of the company and preventing unexpected disruptions. This mission is intricate due to the multifaceted nature of the tasks involved. A significant challenge lies in establishing an effective preventive maintenance framework to minimize downtime. Consequently, the responsibility of the maintenance manager becomes even more significant given the diverse nature of their roles. The primary challenge for the maintenance manager is to enhance efficiency and reduce unplanned downtime through the implementation of proactive maintenance measures.
What is preventive maintenance?
Preventive maintenance, often abbreviated as PM, is a systematic approach employed to maintain machinery, equipment, and assets in a state of optimal functioning. This practice involves regular inspections, servicing, and repairs carried out at scheduled intervals or based on predetermined criteria. The overarching goal of preventive maintenance is to mitigate the likelihood of unexpected breakdowns and failures of various goods, machines, and equipment within an industrial setting.
While the immediate objective of proactive maintenance is to ensure the reliability and longevity of assets, it also plays a significant role in contributing to broader objectives within industrial enterprises. By proactively addressing potential issues and maintaining equipment in good working condition, preventive maintenance helps enhance overall operational efficiency, reduce downtime, and minimize production disruptions. Moreover, it aids in extending the lifespan of assets, thus optimizing the return on investment for the organization.
The diverse nature of industries and the intricate machinery and equipment used within them make preventive maintenance a vital practice for the continued success of growing factories and businesses. It allows companies to stay competitive by avoiding costly downtime, ensuring consistent product quality, and supporting the overall sustainability and growth of the industrial enterprise.
Optimizing Industrial Efficiency: The Role of Preventive Maintenance
In the context of the industrial sector, proactive maintenance is a critical practice that extends beyond machinery and equipment to encompass various aspects of manufacturing and production processes. Here’s an example:
Let’s consider a manufacturing plant that produces automotive components, such as engines and transmissions. In this industrial setting, preventive maintenance is instrumental in ensuring the continuous and efficient operation of the production line.
Machinery Maintenance:
The plant relies on a range of complex machinery, including CNC machining centers, conveyor systems, and robotic assembly lines, to manufacture automotive parts. Preventive maintenance in this context involves regular inspections, lubrication of moving parts, and timely replacement of worn-out components like bearings and belts. By proactively addressing potential issues, the plant can avoid unexpected breakdowns, minimize downtime, and maintain consistent production output.
Quality Control Systems
To maintain high product quality standards, the plant employs quality control systems that include precision measuring instruments and sensors. Preventive maintenance of these systems involves regular calibration and testing to ensure accurate measurements and adherence to quality standards. By preventing inaccuracies and deviations, the plant can avoid manufacturing defects and product recalls.
Facility Infrastructure
Beyond machinery and equipment, proactive maintenance extends to the facility itself. This includes tasks such as inspecting and maintaining the electrical systems, HVAC (Heating, Ventilation, and Air Conditioning) units, and fire suppression systems. Regular checks and servicing of these infrastructure components help prevent unexpected facility disruptions and maintain a safe working environment for employees.
Inventory Management
Effective preventive maintenance also encompasses inventory management practices. Ensuring an adequate supply of critical spare parts is vital to quickly address equipment breakdowns. By regularly reviewing inventory levels and replenishing supplies, the plant can minimize downtime and avoid delays in production.
Training and Skill Development
Preventive maintenance is not limited to physical assets; it also involves investing in the training and skill development of maintenance personnel. Regular training sessions on the latest maintenance techniques and technologies enable maintenance teams to stay up-to-date and efficiently address evolving challenges in the industrial environment.
In the industrial sector, the effective implementation of preventive maintenance strategies ensures that production processes remain reliable, efficient, and cost-effective. It contributes to the overall competitiveness of the manufacturing plant by reducing operational disruptions and optimizing resource utilization.
Strategic Budget Control in Maintenance Management
Maintenance managers face a complex challenge when it comes to managing their department’s budget, with inventory control playing a pivotal role. It is imperative to ensure that all essential spare parts and materials are readily available to facilitate maintenance tasks, preventing unnecessary extensions of scheduled downtime for routine maintenance or unexpected repairs due to equipment breakdowns.
However, an equally significant consideration is avoiding over-purchasing and stockpiling these components, as it can result in wasted capital and resources over time for the organization.
In the realm of budgeting, maintenance managers must adopt a comprehensive approach that encompasses various cost categories, including fixed and variable costs, as well as direct and indirect expenses. They must also engage in effective negotiations with suppliers to secure favorable pricing agreements. Furthermore, they should explore investments in new technological tools capable of enhancing efficiency and delivering tangible value to the organization.
Maintenance Budget Control Dashboard
To effectively control the maintenance budget, maintenance managers can utilize a dashboard that provides real-time insights into key financial and inventory metrics. Here is a simplified example of a maintenance budget control dashboard:
Inventory Status
This section displays the current inventory levels of spare parts and materials. It highlights critical items that are running low, ensuring timely replenishment while avoiding excess stock.

Budget Allocation
A graphical representation of the budget allocation, categorizing expenses into fixed, variable, direct, and indirect costs. This allows managers to monitor and adjust allocations as needed.
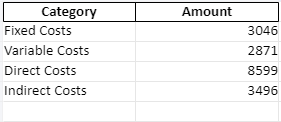
Supplier Negotiations
Tracks ongoing negotiations with suppliers, including pending agreements and cost-saving initiatives. It provides a summary of achieved cost reductions.
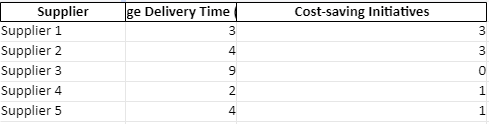
Technology Investments
Shows investments made in technological tools designed to improve maintenance efficiency. It evaluates the return on investment (ROI) and highlights tools that have proven to generate value.
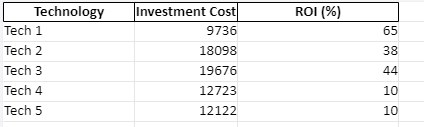
Downtime Impact
Provides data on scheduled and unscheduled downtime and the associated costs, emphasizing the importance of effective maintenance planning.
Historical Expenditure
Compares current budget performance with historical expenditure data, enabling managers to identify trends and areas for improvement.
Budget Variance
Calculates and displays the variance between the allocated budget and actual expenditure, helping managers stay within budgetary limits.
By using such a dashboard, maintenance managers can proactively control their department’s budget, ensuring optimal inventory management and cost-effectiveness while enhancing overall operational efficiency.
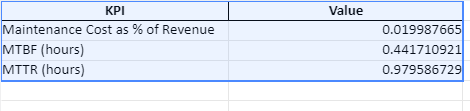
Team Coordination and Efficient Time Management in Maintenance
The organization of maintenance tasks demands leadership and meticulous planning skills. The primary objective is to seamlessly integrate workgroups and allocate tasks based on individual skills, qualifications, and levels of expertise.
Given the diversity in knowledge, experience, and preparedness across technical profiles, collaborative teamwork becomes paramount. It is essential for the maintenance manager to actively foster communication channels, thus promoting a harmonious working environment. This collaboration extends to interactions among team members, between different work teams, and even among various departments involved in maintenance management.
Effective time management is a central facet of this role. Coordinating and overseeing workgroups, task assignments, interactions with suppliers and distributors, addressing inquiries, doubts, and emails, formulating work and maintenance plans, and reacting promptly to unforeseen circumstances constitute a daily routine for every maintenance manager.
The execution of these myriad responsibilities necessitates handling substantial volumes of information, instantaneous access to documents, diagrams, and photographs, as well as the ability to share them efficiently with diverse team members. This approach streamlines the operations of each individual, ensuring the quality and efficacy of their work. Consequently, the effective management of time emerges as a perpetual challenge for maintenance managers.
“Establishing a Comprehensive Preventive Maintenance Strategy and Plan”
To effectively implement a preventive maintenance strategy, it’s essential to monitor your regulatory controls, carry out routine maintenance tasks, and schedule interventions based on the assessment of natural wear and tear on your equipment. In this discussion, we will delve into the three scenarios that necessitate the development of a preventive maintenance plan:
Understanding Preventive Maintenance Strategy
Before creating a proactive maintenance plan, it’s crucial to grasp the fundamental components of a preventive maintenance strategy and the requisite tools to execute it efficiently.
Creating a Preventive Maintenance Plan
Developing a comprehensive preventive maintenance plan involves a thorough understanding of the three primary types of maintenance and how they are put into practice.
In essence, corrective maintenance addresses issues that arise unexpectedly, while preventive maintenance endeavors to prevent such issues from occurring. Corrective maintenance comes into play when equipment experiences sudden breakdowns, whereas preventive maintenance relies on regular inspections and verifications to ensure the proper functioning of assets, aiming to identify and rectify any potential failures before they lead to a breakdown.
Preventive Maintenance Planning:
Before establishing a preventive maintenance strategy, certain prerequisites must be taken into account. proactive maintenance adopts a proactive approach and encompasses four essential action elements: inspection, detection, correction, and prevention. These elements form the foundation upon which an effective preventive maintenance plan is built.
What Are the Key Maintenance Performance Indicators?
Creating a preventive maintenance dashboard in Excel involves various approaches, but it’s essential to understand the primary maintenance indicators commonly utilized by industry professionals. Here, we outline the key maintenance performance indicators:
Planned Maintenance Percentage (PMP)
PMP represents the percentage of time dedicated to planned maintenance activities compared to unplanned maintenance activities. It assesses the degree to which maintenance efforts are proactive versus reactive.
Overall Equipment Effectiveness (OEE)
OEE is a metric used to measure equipment productivity comprehensively. It provides valuable insights into the efficiency of maintenance processes, considering factors such as quality, performance, and equipment availability.
Mean Time to Repair (MTTR)
MTTR serves as a measure of the maintainability of repairable components. It encompasses repair time, the trial period, and the duration required to return the equipment to normal operating conditions.
Mean Time Between Failures (MTBF)
MTBF calculates the expected time between one equipment failure and the next during standard operation. It aids in assessing the reliability and durability of assets.
Compliance of Preventive Maintenance (CPM)
CPM quantifies the effectiveness of preventive maintenance by determining the percentage of planned preventive work completed within a specified timeframe. It evaluates the adherence to scheduled maintenance activities.
In many cases, predefined templates for managing preventive maintenance plans can be obtained, providing an ideal solution for project managers responsible for maintenance planning and scheduling. Excel macros offer a practical option for accessing suitable templates designed to automate asset management, maintain comprehensive records of variables in maintenance plans, and oversee the maintenance of each piece of equipment, among other functions.
The elements of a preventive maintenance dashboard
Maintenance Checklist in Excel is a list with all the actions to be performed in the preventive maintenance plan in Excel. A maintenance checklist is used to ensure:
Constant monitoring of KPIs.
average repair time.
Percentage of scheduled maintenance.
Mean time between failures.
Preventive maintenance dashboard
The Components of a Preventive Maintenance Dashboard
A proactive maintenance dashboard typically comprises various elements aimed at tracking and evaluating maintenance performance. One crucial component is the Maintenance Checklist in Excel, which contains a comprehensive list of actions to be executed as part of the preventive maintenance plan in Excel. This checklist serves several critical purposes, ensuring:
Continuous Monitoring of Key Performance Indicators (KPIs)
The checklist enables the ongoing tracking of essential KPIs related to maintenance operations.
Key KPIs include:
– Average Repair Time
– Percentage of Scheduled Maintenance
– Mean Time Between Failures
Preventive Maintenance Dashboard Task List
The preventive maintenance dashboard includes a task list that provides a detailed breakdown of maintenance activities and their status. It serves as a practical application of the preventive maintenance plan. Here’s an example that illustrates these preventive maintenance indicators:
Imagine a scenario in a factory where maintenance activities were monitored and measured during a specific month:
– Total Scheduled Maintenance Time: 150 hours
– Total Unscheduled Maintenance Time: 40 hours
– Overall Equipment Effectiveness (OEE): 80%
(This implies that the equipment was operational for 80% of the month, with the remaining 20% representing maintenance downtime.)
– Average Repair Time (ART): 3 hours
– Mean Time Between Failures (MTBF): 250 hours
– Compliance of Preventive Maintenance (CPM): 95%
(Indicating that 95% of planned preventive maintenance work was executed as scheduled.)
These figures offer a snapshot of the plant’s preventive maintenance performance for the given month. They provide a means to assess maintenance effectiveness and identify potential areas for enhancement.

Enhancing the Preventive Maintenance Plan Continuously
Maintaining a preventive maintenance checklist is imperative as it facilitates continuous monitoring of KPIs, including average repair time, the percentage of planned maintenance, and mean time between failures. By scrutinizing these statistics and comparing them with previous data, you can gain valuable insights into how your program impacts the efficiency of your maintenance operations. This ongoing analysis allows for adjustments and improvements in the preventive maintenance plan over time.
The Advantages of Preventive Maintenance:
Breakdown Anticipation: Preventive maintenance allows for the anticipation of potential equipment breakdowns, effectively preventing unplanned production stoppages.
Extended Equipment Lifespan: It contributes to prolonging the lifespan of machinery and assets, optimizing their long-term value.
Downtime Reduction: By addressing issues proactively, it minimizes downtime, ensuring continuous operations and productivity.
Quality Customer Service: Maintaining equipment reliability through preventive measures enhances the ability to provide consistent and quality customer service.
Resource Savings: It leads to resource savings by reducing the need for emergency repairs and minimizing the associated costs.
Safety and Compliance: Preventive maintenance ensures that safety standards and compliance requirements are consistently met, mitigating business risks.
When crafting a preventive maintenance plan, it is essential to tailor it to the specific characteristics and needs of your installations and equipment, thus maximizing its effectiveness and benefits. Relying solely on corrective maintenance can pose risks to a business by potentially causing prolonged equipment downtime and compromising maintenance standards, especially in emergency situations.